The Basic Principles Of Alcast Company
Table of ContentsAlcast Company Things To Know Before You BuyThe Main Principles Of Alcast Company Alcast Company - An OverviewThe Best Strategy To Use For Alcast CompanyAn Unbiased View of Alcast CompanyThe 2-Minute Rule for Alcast CompanyAlcast Company for Beginners
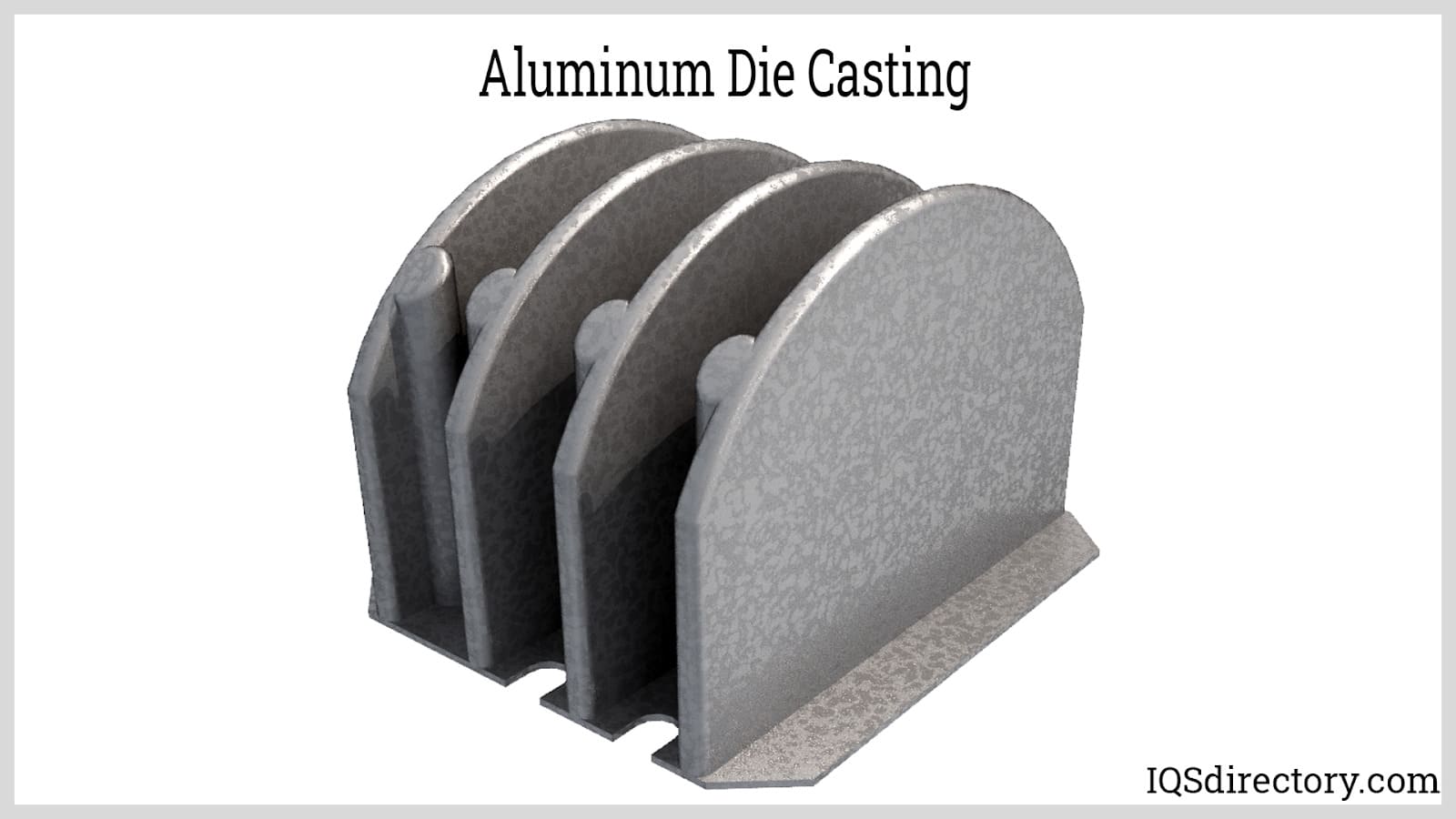
If you think that a wrought alloy may be the most effective for your task, have a look at a few of our articles that discuss more about particular wrought alloys, such as Alloy 6061 and Alloy 6063. On the other hand, if you believe an actors alloy would be much better for you, you can discover more about some cast alloys in our Alloy 380 and Alloy 383 write-ups (coming soon).
Not known Incorrect Statements About Alcast Company

Having the experience and sector knowledge to craft your castings for optimum manufacturing and high quality outcomes will enhance the task. Making aluminum spreading requires a complicated collection of procedures to accomplish the right results. When deciding on a brand-new aluminum foundry to companion with, guarantee they have considerable industry experience and are educated concerning all elements of the light weight aluminum spreading procedure: layout, production, product analysis, and product screening.
(https://replit.com/@reginaldthomas0)The foundry must likewise have a tested record of delivering extraordinary items that satisfy or exceed customer assumptions. Quality assurance ought to likewise go to the top of your checklist when choosing an aluminum factory. By dealing with a qualified foundry who adheres to the standards for quality assurance, you can protect the honesty of your product and ensure it satisfies your specifications.
The Ultimate Guide To Alcast Company
By selecting a firm who uses solutions that satisfy or exceed your item demands, you can be certain that your job will be completed with the utmost accuracy and performance. Particular aluminum foundries concentrate on details kinds of manufacturing processes or casting methods. Various components need different production strategies to cast light weight Discover More aluminum, such as sand spreading or pass away spreading.
Die casting is the name given to the process of producing complicated steel elements via use of mold and mildews of the component, additionally understood as dies. It creates even more components than any type of other process, with a high level of precision and repeatability. There are three sub-processes that fall under the group of die spreading: gravity die casting (or long-term mold spreading), low-pressure die casting and high-pressure die spreading.
No matter the sub-process, the die casting process can be damaged down right into 6 actions. After the pureness of the alloy is examined, dies are developed. To prepare the passes away for casting, it is essential that the dies are tidy, so that no deposit from previous manufacturings continue to be. After cleaning, the ejection lubrication is put on the die to guarantee a smooth release.
The pure metal, also called ingot, is included in the heater and kept at the molten temperature of the metal, which is after that transferred to the injection chamber and infused into the die (Casting Foundry). The pressure is then maintained as the metal solidifies. Once the metal strengthens, the cooling process starts
Not known Facts About Alcast Company
The thicker the wall of the part, the longer the cooling time because of the quantity of indoor steel that also needs to cool down. After the component is fully cooled down, the die halves open and an ejection device pushes the part out. Following the ejection, the die is closed for the following injection cycle.
The flash is the extra material that is cast during the process. Deburring gets rid of the smaller sized pieces, called burrs, after the cutting process.
9 Easy Facts About Alcast Company Explained
However, this proved to be an inaccurate examination, due to the fact that the tester can reduce right into a piece and miss out on an area with porosity. Today, top suppliers utilize x-ray screening to see the whole interior of components without reducing right into them. This permits them to more accurately approve or deny components. To get to the completed item, there are 3 primary alloys used as die spreading material to pick from: zinc, aluminum and magnesium.
Zinc is one of the most used alloys for die casting due to its lower cost of raw materials (Casting Foundry). Its deterioration resistance additionally enables the components to be long enduring, and it is one of the much more castable alloys due to its reduced melting point.
Getting The Alcast Company To Work
As mentioned, this alloy is one of one of the most typically utilized, yet manufactures will, sometimes, choose light weight aluminum over zinc as a result of aluminum's production benefits. Light weight aluminum is extremely cost-effective and among the much more functional alloys. Light weight aluminum is used for a variety of various items and markets anything from home window structures to aerospace materials.